БЛОК ДИЗЕЛЯ, ЦИЛИНДРОВЫЕ ВТУЛКИ И ПОРШНИ
БЛОК ДИЗЕЛЯ И ПОДДИЗЕЛЬНАЯ РАМА
Блок (рис. 40) — это как бы костяк дизеля. Он полностью воспринимает усилия от давления газов на поршни в цилиндрах и силы инерции деталей шатунно-кривошипного механизма, совершающих возвратно-поступательное и вращательное движение.
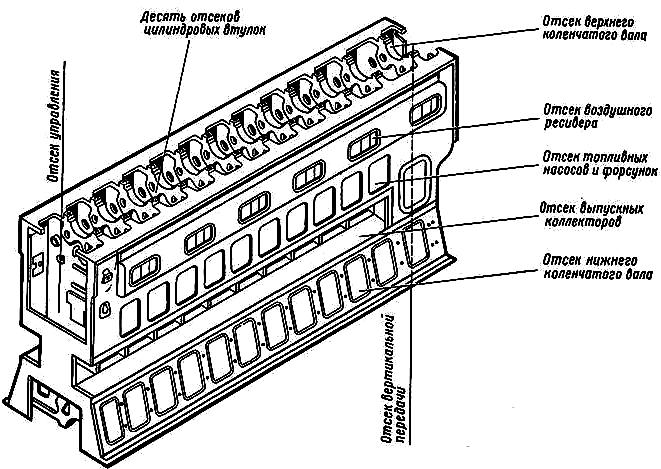
Рис. 40. Блок дизеля 2Д100
К блоку крепят турбокомпрессоры, центробежный нагнетатель, воздухоохладители, топливный, водяной и масляный насосы, форсунки, регулятор частоты вращения и другие вспомогательные агрегаты, механизмы, трубопроводы.
Высокая степень нагруженности блока заставляет конструкторов делать его не только прочным, но и, что особенно важно, жестким. Если блок не будет жестким, он не сможет сопротивляться деформациям, которые могут быть вызваны действием сил и неравномерным нагревом отдельных частей дизеля. В результате может нарушиться работа коленчатого вала и других узлов.
Прочность блока обеспечивает целостность всей конструкции, а жесткость препятствует изменению формы, сохраняя прогибы (деформации) в пределах определенных, допустимых, заранее установленных величин.
По своим размерам блок является самой крупной деталью дизеля. Например, длина блока дизеля типа Д100 около 4 м, ширина — 1,1 м, высота — 1,8 м. Масса блока около 5,5 т.
Чтобы обеспечить блоку дизеля достаточную прочность и жесткость при заданной массе, выбирают не только размеры и форму блока, но и материал. На некоторых дизелях блоки изготовлены из чугуна (например, на дизелях типа Д50), легких алюминиевых сплавов (на дизелях 1Д12, М756 и М753). Блоки дизелей 2Д100, 1 ОД 100, ИД45, 14Д40, Д49 (верхняя часть) и Д70 сварены из листовой стали, что позволяет более рационально использовать металл. Благодаря тому они обладают небольшой массой по сравнению с литыми чугунными блоками, а по массе, приходящейся на 1 кВт, приближаются к блокам из алюминиевых сплавов. В этом состоит одно, из основных преимуществ блоков сварной конструкции.
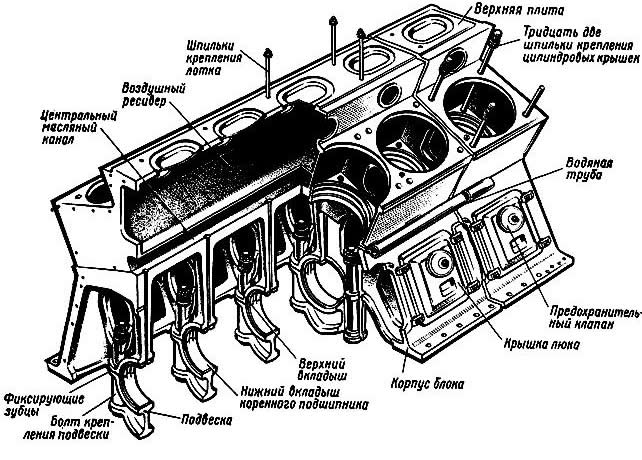
Рис. 41. Блок дизеля типа Д49
Интересно отметить, что длина сварных швов, например блока дизеля 2Д100, достигает 600 м, т. е. в 150 раз больше длины блока, что, конечно, создает трудности в его изготовлении. Блок дизеля типа Д100 представляет собой коробчатую конструкцию из стальных вертикальных и горизонтальных листов с гнездами для цилиндровых втулок и опорами для подшипников верхнего и нижнего коленчатых валов. Листы-перегородки, придавая блоку жесткость, разделяют его по высоте на пять горизонтальных отсеков (см. рис. 40) и по длине на двенадцать вертикальных отсеков, где и размещаются все основные детали и узлы дизеля. Первый (верхний) горизонтальный отсек занимает верхний коленчатый вал; во втором — размещен воздушный ресивер, в который подается воздух для продувки и зарядки цилиндров; в третьем — топливные насосы и форсунки; в четвертом — выпускные коллекторы и в пятом — нижний коленчатый вал. Второй, третий и четвертый отсеки изолированы друг от друга, а первый и пятый связаны между собой через отсек вертикальной передачи и отсек управления. К двенадцати вертикальным отсекам относятся (на рис. 40 справа налево) отсек вертикальной передачи, десять отсеков цилиндровых втулок и отсек управления. Для осмотра и монтажа всех механизмов у отсеков имеются специальные окна-люки, закрываемые крышками. Сверху блок закрыт крышкой картера верхнего коленчатого вала, а снизу блок ставится на поддизельную раму, имеющую картер (корытообразный маслосборник), из которого масло поступает к масляному насосу дизеля. Поддизельная рама состоит из двух массивных продольных балок, соединенных между собой двумя поперечными балками. Для увеличения жесткости поддизельная рама снабжена дополнительными листами (ребрами жесткости). На верхних опорных листах поддизельной рамы имеются отверстия для крепления к ней блока дизеля и станины тягового генератора. Поддизельная рама опирается на раму тепловоза.
Мы подробно рассмотрели устройство блока однорядных дизелей типа Д100. На рис. 41 представлен внешний вид блока V-образного тепловозного дизеля типа Д49. В развале между цилиндрами блока дизеля Д49 образован канал (воздушный ресивер), по которому в цилиндровые крышки (они крепятся к блоку) подается наддувочный воздух. Ниже ресивера размещен центральный масляный канал. К верхней горизонтальной плите блока крепится лоток (на рисунке не показан), в котором установлены распределительный вал, топливные насосы и рычажный механизм привода впускных и выпускных клапанов. Почти такой же внешний вид имеют блоки V-образных двигателей внутреннего сгорания 11Д45 и Д70.
ЦИЛИНДРОВЫЕ ВТУЛКИ
Втулка цилиндра (рис. 42) представляет собой деталь цилиндрической формы. Внутренний диаметр цилиндра дизелей 1 ОД 100 равен 207 мм, дизелей 11Д45—230 мм, Д70—25 мм и Д49—260 мм, а у дизелей Д5О этот диаметр составляет 318 мм.
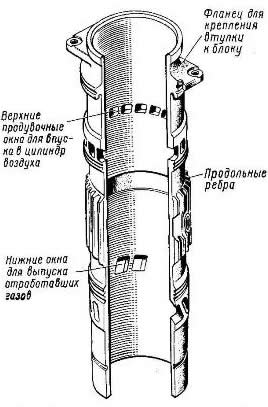
Рис. 42. Втулка цилиндра дизеля 10Д100
Внутренняя поверхность цилиндровой втулки подвергается воздействию высоких температур и давлений газов. Необходимо, чтобы трение поршня о стенки втулки было наименьшим, а кольца поршня всегда прилегали к втулке, обеспечивая хорошую плотность. При этих условиях можно избежать интенсивного износа втулки, поршня и колец. Втулки цилиндров большей частью (дизеля Д100, 11Д45Г Д49, Д50, Д70) отливают из чугуна, легированного, хромом, никелем и молибденом. На некоторых дизелях (1Д12 и М756) втулки изготовляются из стальных труб.
Однако со временем поршень и его кольца при работе дизеля изнашивают поверхность втулки, снимая с нее тонкий слой металла, изнашиваясь в свою очередь и сами. Если бы втулка цилиндра была изготовлена за одно целое с блоком, то при износе ее стенок пришлось бы заменять весь блок, что было бы невыгодно. Поэтому в современных дизелях применяют цилиндровые втулки, которые вставляют в гнезда блока.
Качество внутренней поверхности цилиндровых втулок, в большой степени влияющее на плотность цилиндра, оценивается правильностью геометрической формы втулок и требуемой шероховатостью (чистотой) их поверхности. Какое значение имеют эти требования, можно представить себе, если иметь в виду, что даже тонкое шлифование, оставляющее шероховатость, измеряемую высотой, неровностей 0,12—0,2 мкм (1 микрометр — 1/1000 000 м), не обеспечивает нужной чистоты поверхностного слоя. Для доводки поверхности цилиндровых втулок в качестве основного метода применяется так называемое хонингование (Слово «хонингование» происходит от английского hone — буквально точить, доводить), дающее высоту гребней от 0,05 до 0,1 мкм, т. е. значительно меньшую, чем при шлифовании. После хонингования обработанная поверхность кажется (если посмотреть на нее невооруженным глазом) зеркально-гладкой: ее даже называют зеркалом цилиндра. Чтобы лучше удержать смазку на внутренней (рабочей) поверхности чугунных втулок, часто производят так называемое фосфатирование этих поверхностей (нанесение тонкого слоя фосфатов).
Конструкция втулки в большей степени зависит от типа дизеля (двухтактный или четырехтактный), т. е. от особенностей рабочего процесса двигателя и его теплового режима. Посмотрим как нагружаются различные места втулки. У дизелей 1 ОД 100 и 2Д100 наибольшим тепловым и механическим нагрузкам подвергается средняя часть, так как здесь 'находится камера сгорания.
Другую картину мы имеем у дизелей, скажем, типа Д50, у которых наибольшему нагреванию и наибольшим усилиям подвергается верхняя часть втулки, так как здесь температура и давление газов бывают наиболее высокими. Нижняя часть втулки оказывается в лучших условиях, так как воспринимает меньшие давления и тепловую нагрузку.
Каждая втулка дизеля типа Д100 является общей для верхнего и нижнего поршней. Нетрудно догадаться, что общая прочность втулки мало изменится, если толщину стенки ее уменьшить там, где давление газов меньше. Именно по этим соображениям втулка дизеля Д50 утолщена в верхней части, а на среднюю часть втулки. дизелей типа Д100 напрессована стальная рубашка (необходимая для охлаждения), благодаря чему прочность ее повышена. Местами уплотнения рубашки с втулкой являются специальные цилиндрические пояса, расположенные сверху и снизу от продольных ребер на внешней поверхности втулки.
Втулка должна быть не только прочной, но и жесткой. От нее необходимо интенсивно отводить тепло, образующееся при сгорании топлива, иначе нормальная работа дизеля невозможна. Охлаждение средней части наружной поверхности втулки тепловозных дизелей осуществляется водой. При охлаждении водой температура станок втулок со стороны поршня не должна превышать 150—180°С.
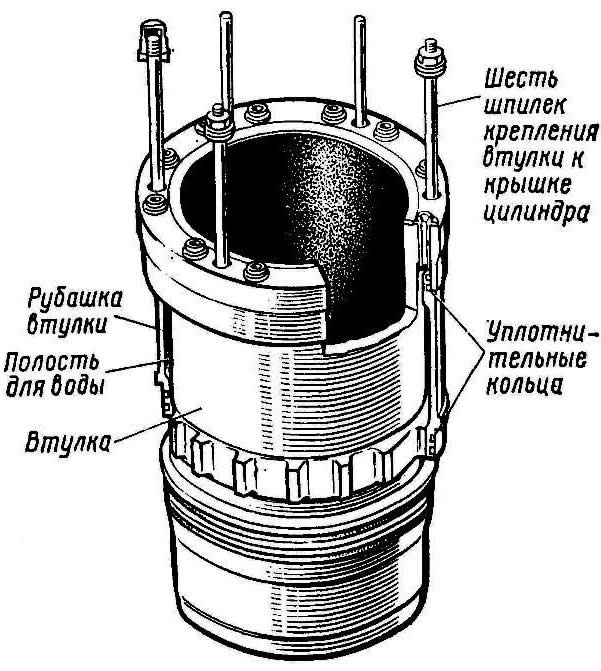
Рис. 43. Втулка цилиндра дизеля типа Д49
При разных режимах работы дизеля температура стенок втулки изменяется в широких пределах. Поэтому втулку в блоке дизеля устанавливают так, чтобы она имела возможность свободно удлиняться. Для этого верхний конец втулки дизеля типа Д100 с помощью шпилек жестко прикреплен к блоку, а щижний конец оставлен свободным, что позволяет ей при нагреве удлиняться вниз.
На рис, 43 показана втулка цилиндра дизеля Д49, конструкция которой получила название подвесной. Втулка соединена с крышкой цилиндра. На втулку напрессована рубашка, вместе с которой втулка вставляется в блок дизеля. Стыки между рубашкой и втулкой уплотняют кольцами. Втулка цилиндра, таким образом, непосредственно к блоку не крепится, а находится в нем как бы в подвешенном состоянии.
ПОРШНИ
Поршень и его детали испытывают при своей работе не только очень высокие тепловые и механические нагрузки, но и перемещаются с большой скоростью. По мере поворота коленчатого вала скорость поршня изменяется от нулевой до наибольшей. Средняя скорость поршней современных тепловозных дизелей находится в пределах 7,2—11,5 м/с. В результате переменной скорости движения возникают и действуют на поршень силы инерции.
В особенно тяжелых условиях находится головка поршня, которая непосредственно соприкасается с горячими газами (температура 1200 — 1800° С). Поршень испытывает большие усилия от действия газов. Так, на головку поршня дизеля Д50, поверхность днища которой составляет примерно 800 см2, действует сила, превышающая 450 Н (46 тс). Эта сила более чем в 2 раза превышает вес самого дизеля с генератором. Не будет преувеличением сказать, что от деталей поршневой группы прежде всего зависит надежность работы дизеля. Однако разработка надежной конструкции поршня оказывается трудным делом: с одной стороны, нужны прочность и жесткость, с другой — легкость: чем меньше вес деталей поршневой группы, тем меньше величина сил инерции, возникающих при движении, тем большую частоту вращения коленчатого вала можно допустить. Положение осложняется тем, что поршень должен интенсивно охлаждаться, иначе из-за высоких температур снизятся прочностные свойства материала, из которого он сделан, и поршень может разрушиться. А отвести тепло от поршня не так просто, ведь он движется.
Стремление обеспечить высокую прочность, легкость и сделать так, чтобы поршень не нуждался в масляном охлаждении, привело к тому, что на ряде дизелей (например, Д50, М756, 1Д12) его изготавливают из алюминиевого сплава (к алюминию добавляют присадки кремния, никеля, марганца и др.). Замечательная особенность этого сплава состоит в том, что он хорошо проводит тепло. Так, если при наибольшей нагрузке дизеля головка алюминиевого поршня нагревается до 300° С, то этот же поршень из серого чугуна имел бы температуру около 500° С, требующую уже специального (масляного) охлаждения.
Чугун проводит тепло в три раза хуже, чем поршневой алюминиевый сплав. Если к этому добавить, что алюминиевый сплав в 2,6 раза легче чугуна, то станет ясно, почему поршни дизелей многих марок изготовлены из сплавов на основе алюминия.

Рис. 44. Поршень дизелей 10Д100 и 2Д100 безшпилечной конструкции
У различных тепловозных дизелей поршни могут отличаться друг от друга конструкцией, материалом и размерами, но все они по своей форме напоминают стакан (рис 44), высота которого почти всегда больше диаметра. По своей форме поршни дизеля не являются строго цилиндрическими. Если бы поршень по всей длине имел одинаковый наружный диаметр, то его головка, которая работает в зоне высоких температур, расширилась бы больше, чем нижняя часть, что привело бы к заклиниванию поршня в цилиндровой втулке. Чтобы этого не произошло, диаметр головки поршня при изготовлении несколько уменьшают по сравнению с диаметром нижней части его, называемой юбкой, т. е. придают поршню коническую форму. Такой поршень при нагревании приобретает форму, близкую к цилиндрической. Боковая поверхность поршней современных дизелей имеет весьма сложную геометрическую форму, образованную из ряда конических и цилиндрических поверхностей. Сторона поршня, обращенная к камере сгорания, обычно делается вогнутой, что улучшает условия сгорания топлива.
Рассмотрим вкратце устройство поршня дизелей Д100 (см. рис. 44). Главными деталями его являются корпус (стакан) с днищем вогнутой формы и вставка, которая соединяется с корпусом с помощью пружинного стопорного кольца. Корпус поршня изготовлен из серого чугуна, легированного хромом, никелем, молибденом и медью; сделано это для повышения прочности материала. Вставка имеет два отверстия, в которые запрессованы бронзовые втулки; в них вставлен поршневой палец. Средней частью палец входит в верхнюю головку шатуна. Такая конструкция поршня называется составной. При составном поршне камера сжатия дизеля может быть изменена за счет регулировочных прокладок разной толщины (от 0,1 до 3,0 мм), устанавливаемых между вставкой и верхней и нижней плитами. Такое соединение корпуса поршня со вставкой (без шпилек) возможно только в двухтактных дизелях, где силы давления газов всегда прижимают корпус поршня к вставке, так как они превышают силы инерции. Начиная с 1974 г. бесшпилечные поршни устанавливают серийно на дизелях 10Д100 и 2Д100.
Составную конструкцию имеет и поршень двухтактного дизеля 11Д45, у которого вставка с корпусом поршня соединена также с помощью стопорного кольца.
На четырхтактных дизелях Д49 головка поршня, изготовлена из жаростойкой стали, соединяется с тронком поршня из кованого алюминиевого сплава с помощью четырех шпилек.
ПОРШНЕВЫЕ КОЛЬЦА
Поршень, перекрывающий поперечное сечение цилиндра, должен быть устроен так, чтобы через зазор между поршнем и стенками цилиндра в картер дизеля не проникали газы. Утечка газов приведет к снижению мощности дизеля. Кроме того, газы, проходя через зазор, вызовут местный перерыв стенок цилиндровой втулки и выгорание масла. Это повлечет за собой интенсивный износ втулки и поршня. Утечка же воздуха при ходе сжатия приведет к снижению экономичности, а температура, в камере сгорания может оказаться недостаточной для воспламенения топлива.
Для чего в таком случае нужен зазор? Если его не предусмотреть, то во время работы дизеля поршень расширится и его заклинит в цилиндровой втулке; зеркало ее и боковая поверхность поршня будут повреждены. Чтобы этого избежать, между поршнем и втулкой цилиндра приходится оставлять зазор, а конструкцию поршня несколько усложнять: и а его поверхности протачивают кольцевые канавки (ручьи) (см. рис. 44), в которые вставляют упругие (пружинящие) уплотнительные кольца (рис. 45).
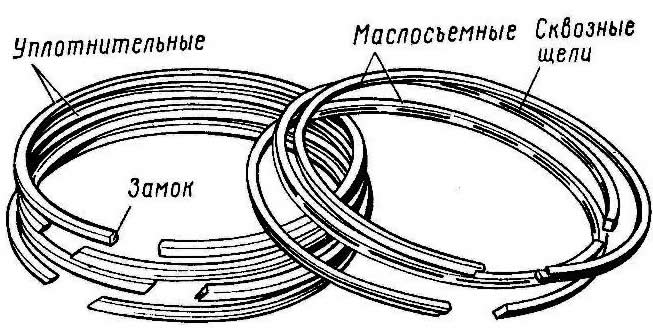
Рис. 45 Кольца поршня дизеля 10Д100
Первое требование к кольцам — это плотное прилегание к канавкам поршня и боковой поверхности цилиндровой втулки. В свободном состоянии диаметр кольца больше, чем диаметр втулки: все кольца имеют разрез - замок (см. рис. 45). Замок позволяет разжать кольцо и в таком состоящий надеть его на поршень. Такие упругие кольца, заведенные вместе с поршнем во втулку, подобно пружине стремятся разжаться и при этом плотно прилегают к стенкам цилиндровой втулки. В сжатом состоянии в месте стыка концы кольца сходятся. Формы замков бывают разными. Наибольшее распространение получили косые замки. Под давлением воздуха и газов кольца плотно прижимаются к канавкам поршня и, кроме того, прижимаются к боковой поверхности втулки, обеспечивая достаточную герметичность (уплотнение) внутри цилиндра.
Когда в процессе работы зазор между поршнем и цилиндровой втулкой вследствие износа увеличивается, поршневые кольца, будучи упругими, разжимаются, чем достигается самоуплотнение их во втулке. Уплотнительные (компрессионные) кольца размещены в верхней части поршня, а самое верхнее - вблизи днища поршня. Поршни дизелей 1 ОД 100, 2Д100, 14Д40, 11Д45 имеют по четыре канавки для уплотнительных колец, поршни дизелей Д49 и Д70 — по три канавки, а поршни дизелей 2Д50 и Д50 - по пять.
Несколько колец, расположенных рядом, создают лучшую преграду (по сравнению с одним кольцом) против проникновения (пробоя) газов в картер дизеля (во время рабочего хода поршня) и против утечки воздуха из цилиндра (во время сжатия).
Работа уплотнительных колец сопровождается интересным явлением. Взгляните на рис. 46, а.
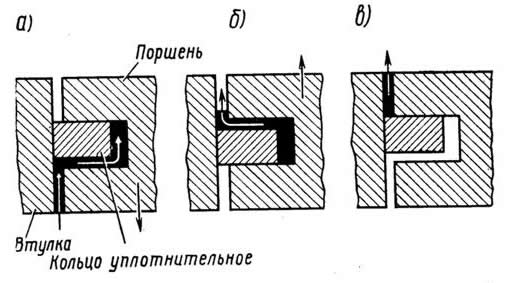
Рис. 46. Схема насосного действия уплотнительных колец
Когда поршень начинает перемещаться вниз, уплотнительные кольца прижимаются к верхней плоскости канавки поршня так, что между нижней и боковой плоскостями каждого кольца и канавками образуется, свободное пространство, которое заполняется маслом. При движении поршня вверх (рис. 46, б) кольца прижимаются к нижней плоскости канавок, и они выжимают попавшее в канавки масло кверху, в камеру сгорания.
Масло, находившееся под кольцом, оказывается над кольцом. Получается, что поршневые кольца, прижимаясь поочередно к верхней и к нижней плоскостям канавок, то засасывают масло, то постепенно вытесняют его (рис. 46, в) в камеру сгорания подобно насосу. «Насосное действие» колец настолько сильно, что на внутреннюю поверхность цилиндра поступает масла больше, чем требуется, а это нежелательно, так как избыток масла попадает в камеру сгорания, оставаясь на стенках цилиндра. Масло подвергается нагреву от горячих газов. Так как оно находится на относительно холодных стенках, то полностью не сгорает и превращается в смолистое вещество, которое в виде нагара после остановки дизеля затвердевает на головке поршня, забивает канавки в зазорах между поршнем и поршневыми кольцами, ухудшает подвижность уплотнителышх колец.
Нижняя часть зеркала цилиндровой втулки покрывается слоем масла, попадающего на стенки втулки через зазоры подшипников шатунно-кривошипного механизма путем разбрызгивания. Как же снять с зеркала втулки избыток масла? Для этого поршень снабжают еще двумя-тремя маслосъемными (или маслосрезывающими) кольцами, устанавливаемыми в нижней части поршня.
Конструктивно маслосъемные кольца отличаются от уплотнительных еще и тем, что имеют скошенную острую кромку (рис. 47), которой при движении поршня вниз от камеры сгорания) они соскабливают масло со стенок цилиндровой втулки. Дальше через сквозные щели в кольце и каналы в кольцевых канавках поршня масло стекает в картер дизеля.
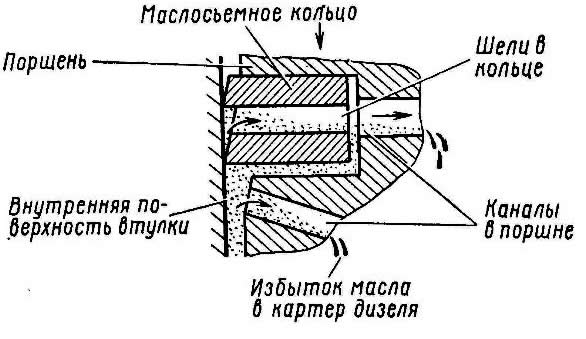
Рис. 47. Схема работы маслосъемного кольца
При обратном ходе, когда поршень движется вверх к камере сгорания, кольцо своими скошенными поверхностями скользит по масляной пленке, но не может его увлечь. Поршень дизеля 10Д100 наряду с масло-съемными кольцами, имеющими щели, снабжен также кольцами без щелей. В последнем случае масло, срезаемое кольцом, стекает в картер через отверстия в теле поршня.
ПОРШНЕВЫЕ ПАЛЬЦЫ
Усилия от поршня к коленчатому валу передаются через поршневой палец, шарнирно соединяющий поршень с шатуном. Общим у пальцев дизелей 10Д100, 11Д45, Д50 является то, что они выполнены полыми. Это сделано для облегчения веса, а у дизелей типа Д50 — и для подачи смазки к трущимся поверхностям. Палец шпилечного поршня дизеля 2Д100 по способу закрепления отличается от пальца дизеля Д50. При работе дизеля Д50 палец может свободно поворачиваться, а при работе дизеля 2Д100 палец остается неподвижным относительно вставки поршня — он закреплен во вставке. Если палец при работе может свободно поворачиваться в поршне и головке шатуна, то он называется плавающим. Плавающие пальцы изнашиваются почти равномерно по всей поверхности благодаря тому, что имеют возможность поворачиваться. Эта особенность имеет важное значение, так как при неравномерном износе образуются односторонние зазоры между пальцем и головкой шатуна. Чем больше зазор, тем с большей силой ударяет палец о втулку шатуна, изнашивая ее и создавая повышенные напряжения в шатунно-кривошишюм механизме.
В начало статьи
<< Назад --------------------------------- Дальше >>
|
|